こんなお困りはありませんか?
-
機械加工において
切削工具の異常による
(摩耗、チッピング、折損など)
加工不良を無くしたい -
マシニングセンタでの
工具切り替え時の
偏心による加工不良を
無くしたい -
工具寿命を延長して工具
コストを下げるとともに、
段取り時間を削減し
設備の稼働率を上げたい -
異常発生時の
原因解析を
もっと楽にしたい
リコー独自開発の振動センサと専用コントローラによる
モニタリングシステムがあなたの悩みを解決します!
-
POINT1
リコー独自の広帯域高感度振動センサーとAI解析モデルで、切削工具の異常を検知。加工不良を抑制
-
POINT2
工具装着時の切粉の嚙み込みによる偏心を加工前に検知。加工不良を未然に防ぎます。さらに加工中も偏心が無いかのモニタリングが可能
-
POINT3
切削工具のTBM(Time Based Maintenance)からCBM(Condition Based Maintenance)への移行を振動モニタリングで実現
-
POINT4
振動データは切削区間ごとに自動的に可視化・整理されて保存されるので、異常発生時の振動データの振り返りが容易
システムの特長を動画でチェック
ファナック製ロボドリルなどのマシニングセンタの振動データを
FFT解析などにより視覚的にモニタリング
ファナック製のマシニングセンタ「ロボドリル」をはじめとしたファナック製CNC採用のマシニングセンタに取付可能※。振動センサーは主軸側面などに設置します。ロボドリルに取り付けた場合は、ロボドリルのメニュー画面上で振動の波形やFFT(Fast Fourier Transform)解析による周波数成分(スペクトログラム)、切削区間の表示が可能です。
※ロボドリル以外のファナック製CNC採用のマシニングセンタへの取付には別途実機確認が必要です。
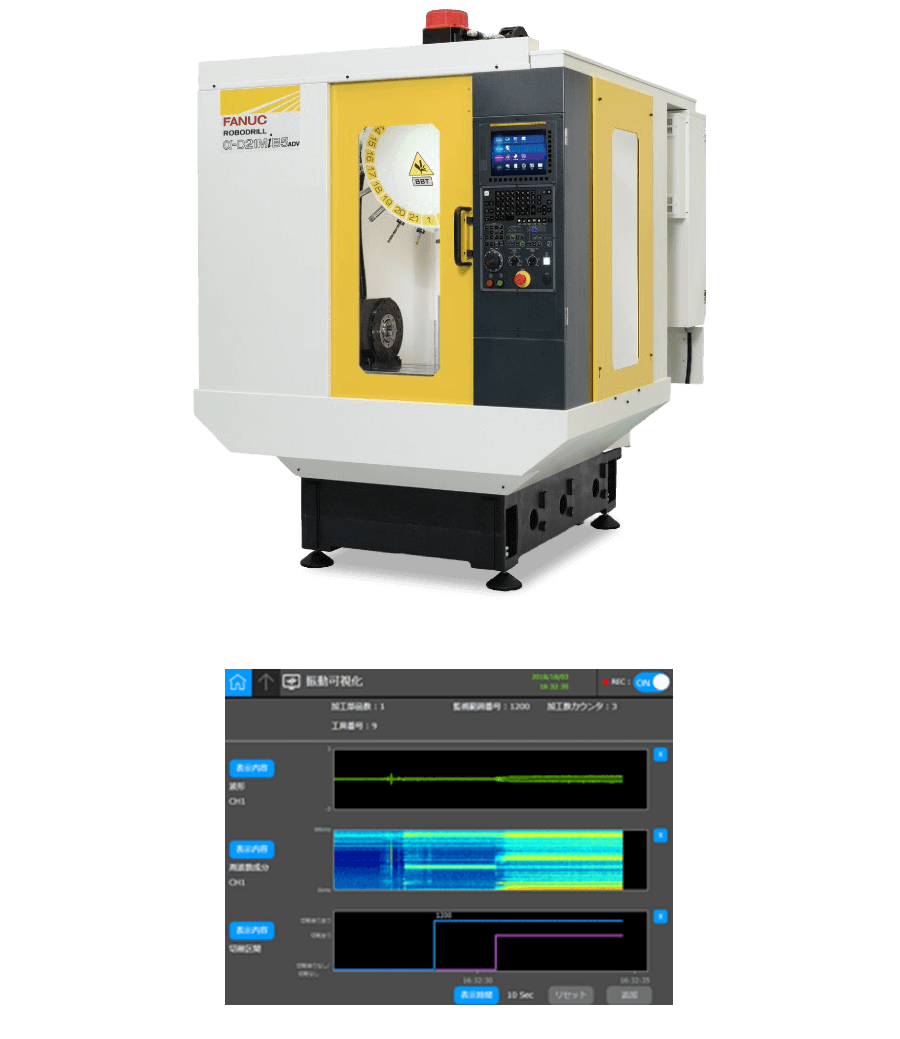
ドリル、リーマー、フライス、タップといった切削工具の、
摩耗・欠け(チッピング)・折損や偏心を
リコー独自開発の振動センサーを使って検知
マシニングセンタで使用するドリル、リーマー、フライス、タップといった切削工具の、摩耗・欠け(チッピング)・折損や偏心をリコー独自開発の広帯域高感度振動センサーで検知※。10Hzから96kHzまでの幅広い周波数帯域の振動をリアルタイムにモニタリング可能です。
※切削工具の刃径によっては検知が難しい場合があります。
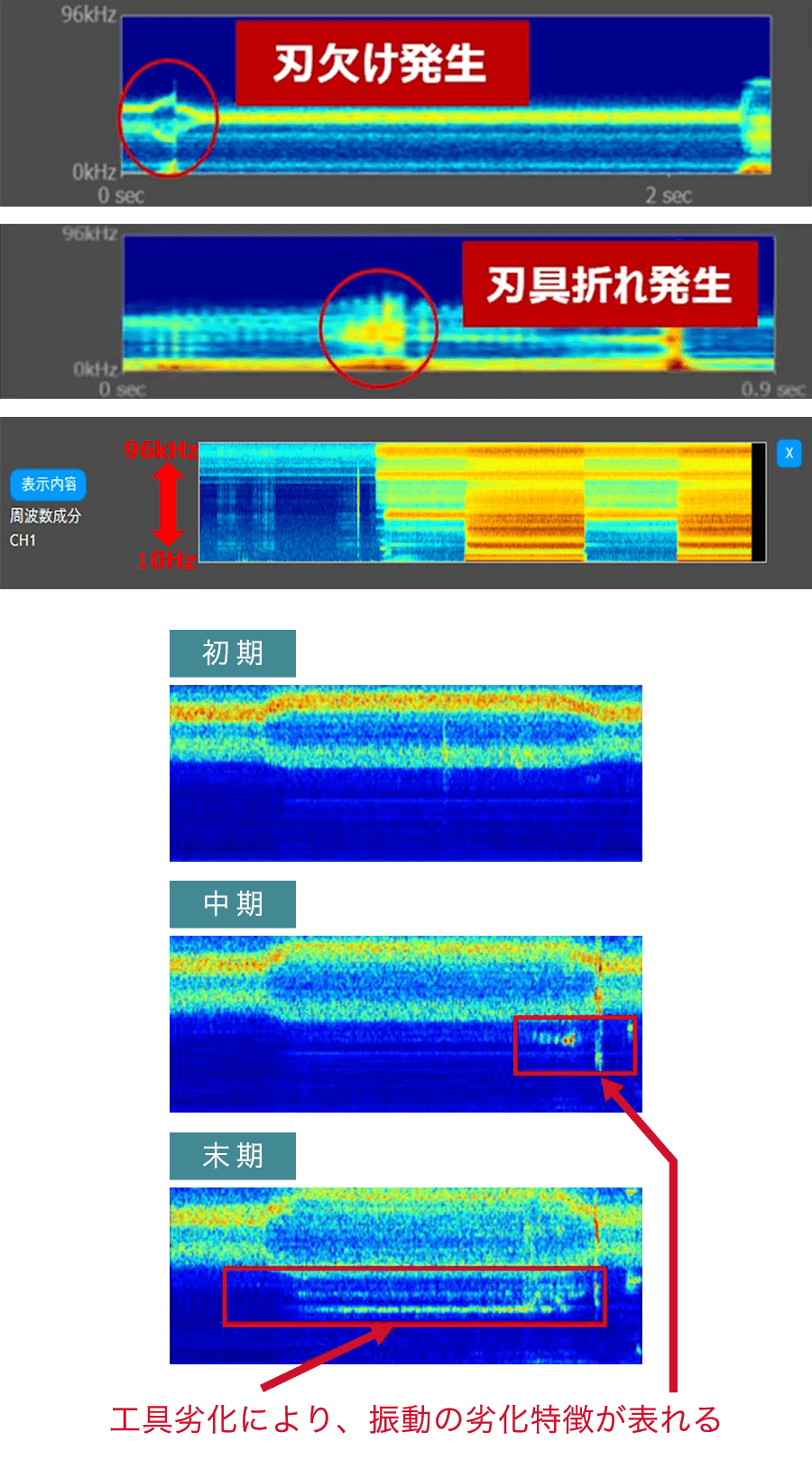
リコー独自のAIモデルで、
切削工具の「TBM」から「CBM」への転換をお手伝い
正常加工の振動データを10回程度、AIで機械学習。モニタリングしたい異常(摩耗、チッピング、折損、偏心、主軸異常など)ごとに開発したリコー独自のAI解析モデルで振動データを自動でスコア化。一定のスコア(閾値)を超えたら異常アラートを出力したり、マシンを停止するように設定可能です。異常の有無にかかわらず定期的に切削工具を交換する「TBM」から、異常の予兆を察知して切削工具を交換する「CBM」を実現します。
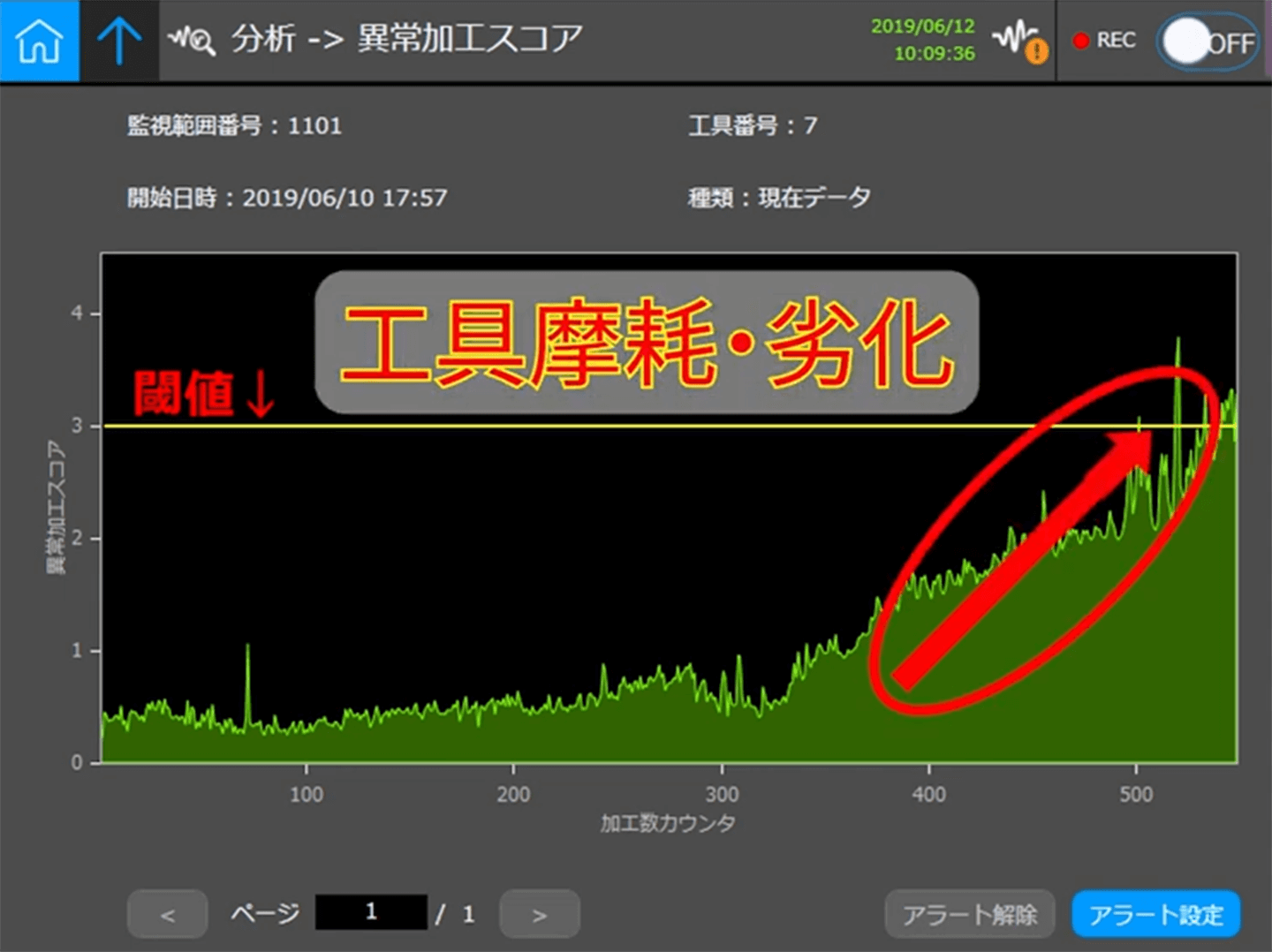
TBMとCBM
機器や工具が故障や破損してからメンテナンスや部品交換をおこなう事後保全と異なり、TBM(Time Based Maintenance)もCBM(Condition Based Maintenance)も、機器が故障する前に予防的にメンテナンスや部品交換ををおこなう予防保全の一種です。TBMは、あらかじめ定めた周期(部品や工具の寿命を想定)ごとに故障する前に整備や保全交換を行う方式をいいます。これに対し、CBMは機器や工具の劣化状態をモニタリングし、一定以上の劣化を確認したら故障する前に交換する方式です。CBMには例えば摩耗する工具であればその長さを測定し、一定の摩耗が検知されたら交換するという、直接的に劣化状態をモニターして交換する方法と、振動や電流値といった設備故障に関係するパラメーターをセンサーなどで計測し、それらの変化から故障や摩耗の予兆を感知した時点で保全交換する予知保全といった概念が含まれます。
故障してから部品や工具を交換する事後保全と比べると、TBMは機器故障による急なラインストップなどを防げるメリットがありますが、余裕を持って交換タイミングを短めに設定すると、まだ使える部品や工具を交換することになり部品や工具の交換コストが上昇します。逆に交換周期を長めに設定すると、部品の故障頻度のばらつきにより、機器によっては交換周期より前に故障してしまい、ラインストップが発生します。このあたりの交換周期の決定がTBMの難しさでもあります。
これに対し、CBMは機器や工具の故障や破損に至る進行度合いを振動や電流値などをセンサーでモニターしているので、適正なタイミングで部品や工具の交換が可能です。その結果、交換頻度の低減によるコスト抑制と、急なラインストップによる生産性の低下防止を同時に実現することができます。良いことずくめのように見えるCBMですが、状態モニタリングのためのセンシング機器の導入等の設備投資や、センサーデータの分析などが必要になります。
振動データは外部のNASや
RICOH振動分析サーバーVAS-10で蓄積可能
ファナック製CNCとの連携により、使用工具や実切削区間などの加工情報と振動データとを紐づけて振動データが保存されるので、前加工無しで見たい工具や切削区間を指定して振動データを参照したり比較することが可能です。
また振動データは外部のNASやRICOH振動分析サーバーVAS-10で蓄積可能。過去の振動データを振り返って比較参照することもできます。
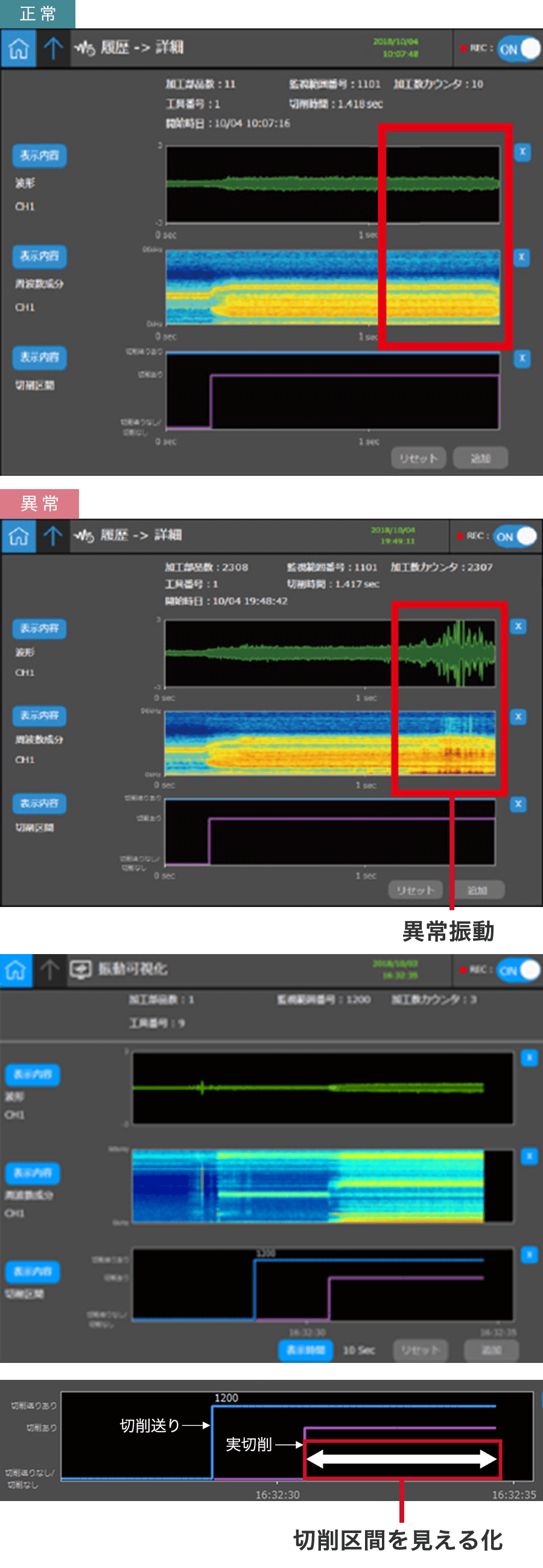
振動データは切削区間などの加工情報の紐づけが可能。過去データの参照や比較も容易
工具摩耗の振動例
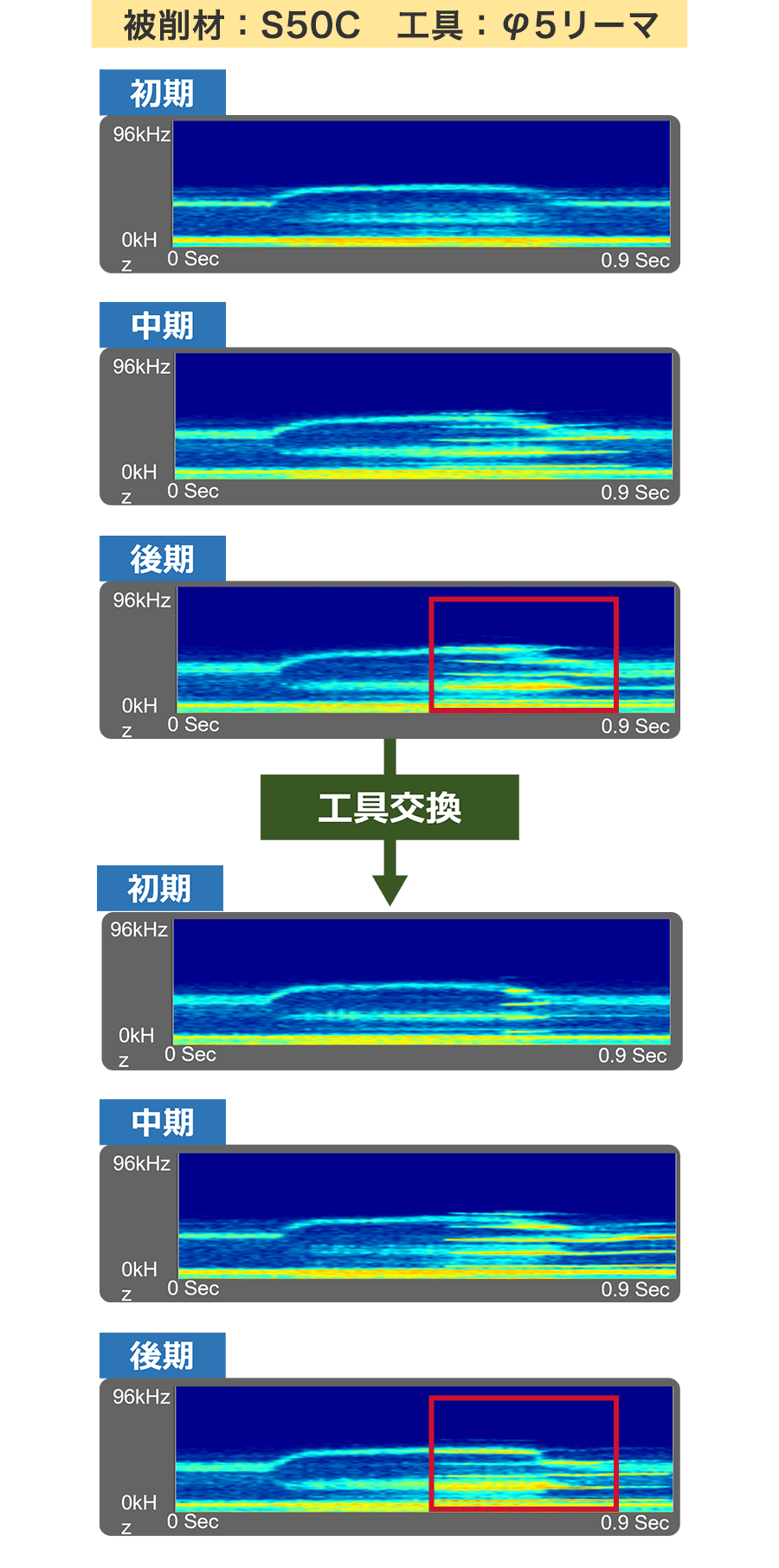
ドリルの摩耗により切り屑の排出変化が発生
これにより、切削終了間際の振動が変化している
工具寿命の延長/適正化が期待でき、工具費用や工具交換時間の削減が可能
工具折損の振動例
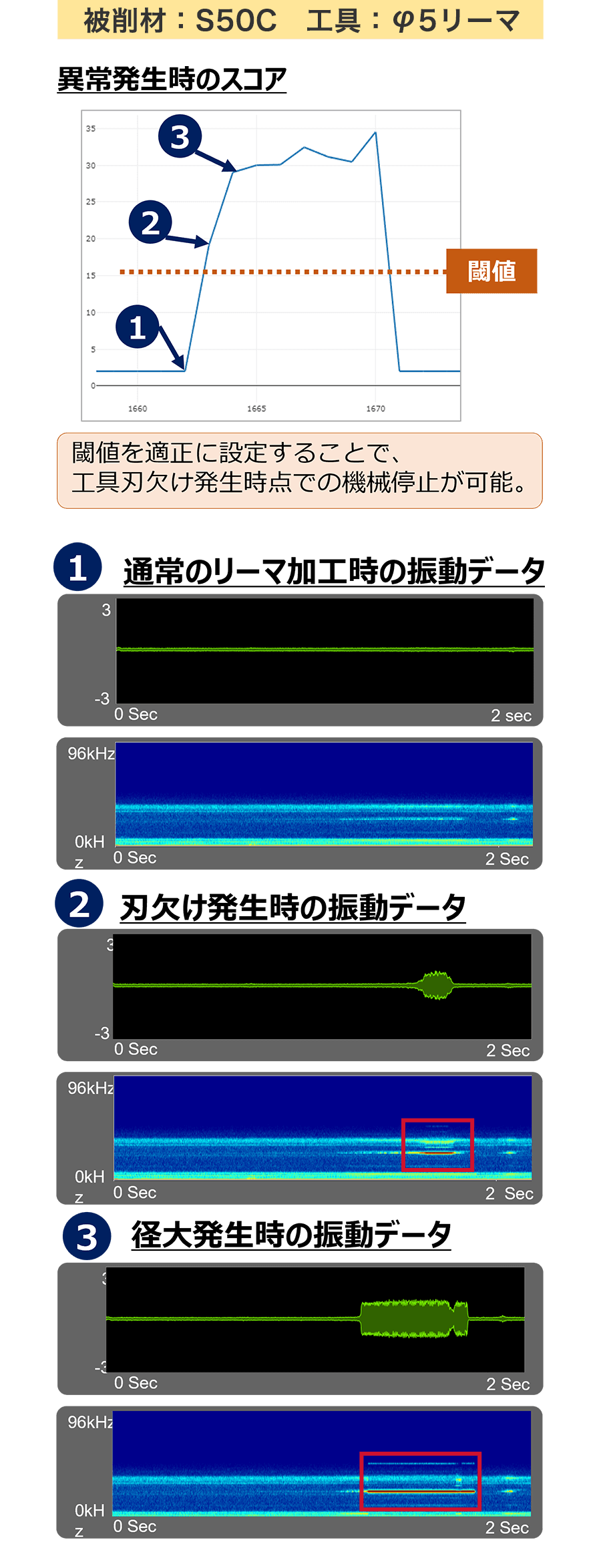
リーマの欠けによる径大発生時の振動変化を確認
刃欠け発生時にアラート機能で機械停止
不良品の生産を防止
偏心の振動例
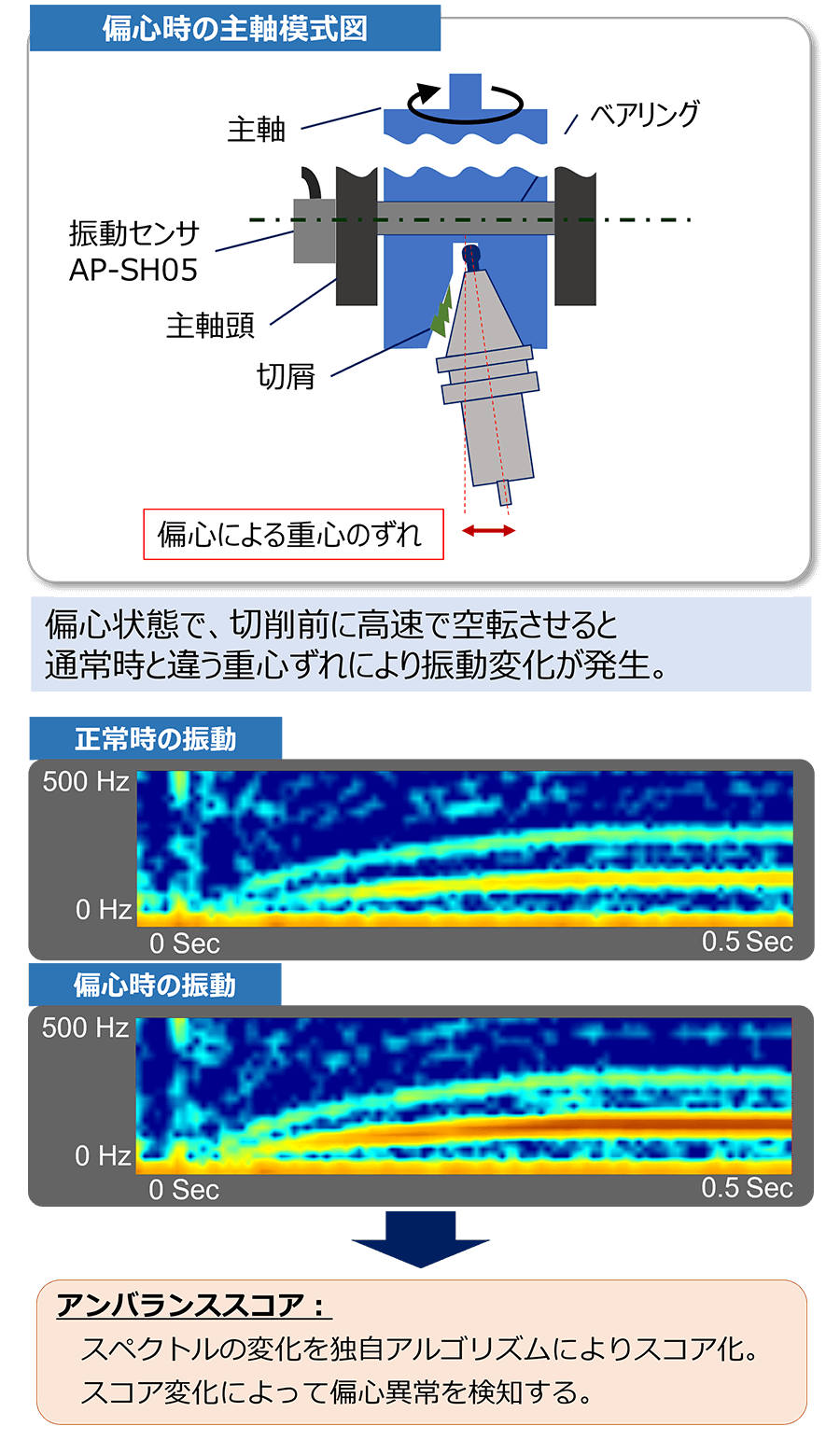
偏心状態で切削前に高速回転させると重心のずれにより振動変化が発生
スペクトルの変化を独自アルゴリズムによりスコア化
スコア変化によって偏心の異常を検知
システム導入による、製品の品質 / 生産性向上
ランニングコストの適正化を叶えます。
- 工具交換頻度の減少、工具使用本数の
低減によるコスト削減 - 不良発生による急な生産ラインストップの防止
- 熟練工による属人的な切削工具の異常検知を
AIにより機械化可能
加工中の状態把握や工具の確認などの作業は、これまで熟練工の経験値や勘・コツといった能力に頼ってきた部分がありますが、熟練工の高齢化や慢性的な人手不足などでこれらの知見をどのように機械化していくかといった課題があります。リコーの振動モニタリングシステムは、振動データをAI処理し、熟練工の経験値や勘を、AIが算出する異常加工スコアに結び付けて置き換えることで、熟練工の知の継承と機械化を同時に実現することが可能です。
一方、折損や工具摩耗、チッピングによる加工不良の発生を未然に防止するため、生産工程では工具の定期的な早期交換などの予防保全で対応していますが、工具交換頻度や工具費・判定作業工数などの増加が課題となっています。
振動モニタリングシステムAP-10Fは、切削振動の可視化により切削工具の異常を判定。工具交換時期を最適化し、工数や費用の削減に貢献します。また、工具取付時の偏心による加工不良も防止します。
モニタリングシステム製品構成
-
リコー振動センサ
RICOH AP-SH05
(標準タイプ)(マグネットタイプ) -
専用コントローラ /
専用ソフトウェアRICOH AP-10F
-
ファナック製ロボドリル
FANUC
※RICOH AP-10Fとファナック製ロボドリルの間には、下記が必要です。
イーサネットケーブル1:機械の情報取得用
イーサネットケーブル2:モニター画面出力用
I/Oケーブル:PMC信号取得/電源起動用
取り付け例
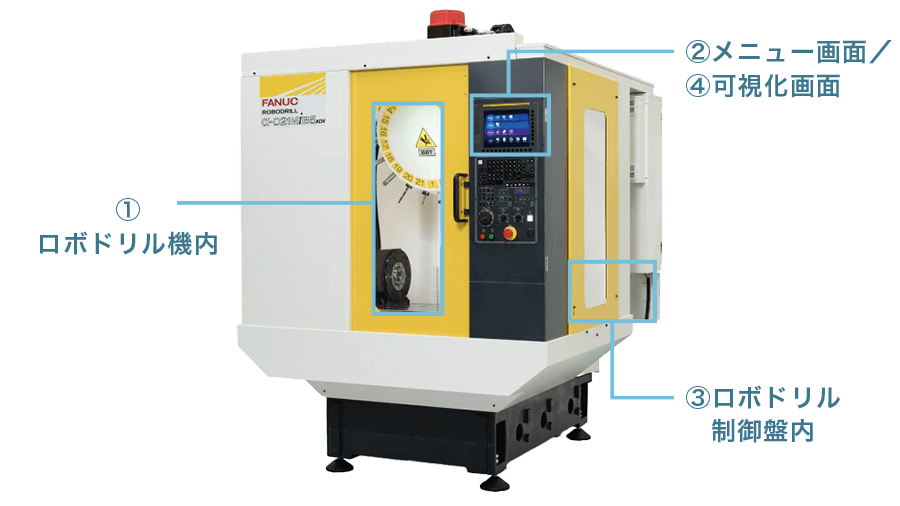
※iHMI 搭載の場合、リモートデスクトップ機能により CNC 画面に表示可能
-
①ロボドリル機内
-
②メニュー画面
-
③ロボドリル制御盤内
-
④可視化画面
オプションのご紹介
AP-10Fで収集した加⼯時に発⽣する振動データをサーバーに蓄積し、リコー独⾃の AI がわかりやすくスコア化。過去データの比較や参照が容易にできます。
データから加⼯不具合や⼯具寿命を分析でき、品質向上とコスト適正化をサポートします。
導入されたお客様の声
自動車メーカーA社様
切削工具の摩耗状態を可視化し、工具交換タイミングを最適化することで、工具寿命約30%延長に成功。工具寿命延長による工具費削減、および交換作業や品質確認工数を削減することで、約400万円/年の改善効果を見込んでいます。
自動車メーカーB社様
チッピングによる微細な振動の変化を可視化し、チッピングによる径大発生を検知することができました。その結果、加工異常の早期発見による仕損費の低減を実現しました。
自動車メーカーC社様
人手によるワーク投入ライン(量産ライン)における加工済みワーク再投入による二度加工(空加工)の異常検知による不具合流出防止に成功。不具合対応工数の削減、Fコスト低減を実現しました。
社内事例
切削振動可視化により工具交換頻度や工具使用本数を削減、さらに工具摩耗判定で判定作業の省人化に成功。
約200万円のコスト削減を実現しました。